Friday, January 27, 2012
Updated Colour Formulations - System B3 Aqua
We have updated our B3 Aqua Color Mixing System with a brand new updated mixing book (colour formulations)
The new pdf. file can be downloaded from our official HBC website by registered users here
If you have purchased a HBC system and would like to register please view our guide on how to register your system here
Base colours mixing system for Plastic, Leather & Vinyl
System B3 Aqua works on all flexible, hard and soft materials basecolours for mixing of plastic-, leather- and vinyl colours. Incl. colour swatch, formulas and additives. Exists as water based.
The complete dye to match-system for all soft, hard, and flexible materials such as leather, fabric, vinyl, plastic, and glass fibre.
The standard system includes colour swatch, gloss system, mixing book, and primers, etc. All dyes and glosses gain a permanency that makes this system indispensable for service mechanics working with the repair of plastics or with maintenance jobs on furniture, cars, lorries, etc..
Colour matching system with additional spectrophotometer & software
download HBC's scanner information
Colour matching system with system B3 Scan is a simple process with the new developed spectrophotometer. Simply place the spectrophotometer directly on the dashboard, leather or vinyl surface and scan. A few minutes after the scan the software gives you the complete mixing receipt.
Colour Matching System
HBC system Smarttool Production introduces an exciting solution to an age-old problem of getting the new colour to exactly and invisibly match the existing original panel.
Using sophisticated colour analysis software and professional spectrophotometer equipment we can provide the exact "recipe" to deliver perfect colour matches every time.
How does the smart repair color matching kit work?
The original leather and vinyl is "scanned" with the hand-held spectrophotometer. The resulting data is converted into an easy to follow recipe drawing on 5 of the 13 "base" B3 scan colors. The list of standard colours made by HBC system, is also available to download on www.hbc-system.com
The recipe gives the exact amount of each colour that is needed to achieve the volume required, from as little as 50ml to 5 litres per mix.
All that is needed is to measure and mix the colours thoroughly, add the right level of dulling agent (gloss adjuster) to adjust the sheen to the correct level. Now you are ready to paint the repair area.
Color matching system’s key advantages:
Exact match of every pigmented and aniline leather and vinyl
Eliminate waste of colours necessary with manual colour matching to reach the correct one
Dramatically time reducing. Gives perfect results in seconds not hours
Improve sales margin on restoration & colour matching works
Doesn’t need computer experience, user friendly software interface
Very light and portable hardware solution, ideal for mobile workers
Improve work time management, you are sure to complete the colour matching in minutes
Clean, fast and easy colour matching process
Greatly reduce necessary skill request to realize perfect colour matching
Full capable PC running standard Windows software
You can have all this functionalities in your handled device or your PC!
By using the B3 scan colour system technics you will be able to get faster and better results, saving money and getting more satisfied customers.
The B3 scan colour system is currently used by many satisfied customers and partner worldwide, providing the leather technicians, furniture producer and car interior repairer a much higher profit margin and happy customers!
B3 Aqua and B3 Scan are available in 250 ml. 1, 5, & 15 Liter bottles
The Spectrophotometer for color mixing can be ordered online on this link
The complete dye to match-system for all soft, hard, and flexible materials such as leather, fabric, vinyl, plastic, and glass fibre.
The standard system includes colour swatch, gloss system, mixing book, and primers, etc. All dyes and glosses gain a permanency that makes this system indispensable for service mechanics working with the repair of plastics or with maintenance jobs on furniture, cars, lorries, etc..
Colour matching system with additional spectrophotometer & software
download HBC's scanner information
Colour matching system with system B3 Scan is a simple process with the new developed spectrophotometer. Simply place the spectrophotometer directly on the dashboard, leather or vinyl surface and scan. A few minutes after the scan the software gives you the complete mixing receipt.
Colour Matching System
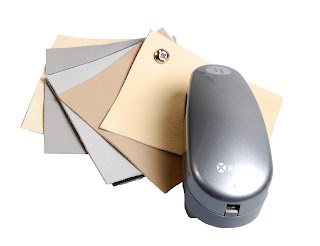
Using sophisticated colour analysis software and professional spectrophotometer equipment we can provide the exact "recipe" to deliver perfect colour matches every time.
How does the smart repair color matching kit work?
The original leather and vinyl is "scanned" with the hand-held spectrophotometer. The resulting data is converted into an easy to follow recipe drawing on 5 of the 13 "base" B3 scan colors. The list of standard colours made by HBC system, is also available to download on www.hbc-system.com
The recipe gives the exact amount of each colour that is needed to achieve the volume required, from as little as 50ml to 5 litres per mix.
All that is needed is to measure and mix the colours thoroughly, add the right level of dulling agent (gloss adjuster) to adjust the sheen to the correct level. Now you are ready to paint the repair area.
Color matching system’s key advantages:
Exact match of every pigmented and aniline leather and vinyl
Eliminate waste of colours necessary with manual colour matching to reach the correct one
Dramatically time reducing. Gives perfect results in seconds not hours
Improve sales margin on restoration & colour matching works
Doesn’t need computer experience, user friendly software interface
Very light and portable hardware solution, ideal for mobile workers
Improve work time management, you are sure to complete the colour matching in minutes
Clean, fast and easy colour matching process
Greatly reduce necessary skill request to realize perfect colour matching
Full capable PC running standard Windows software
You can have all this functionalities in your handled device or your PC!
By using the B3 scan colour system technics you will be able to get faster and better results, saving money and getting more satisfied customers.
The B3 scan colour system is currently used by many satisfied customers and partner worldwide, providing the leather technicians, furniture producer and car interior repairer a much higher profit margin and happy customers!
B3 Aqua and B3 Scan are available in 250 ml. 1, 5, & 15 Liter bottles
The Spectrophotometer for color mixing can be ordered online on this link
Balancing Powder
− a high-quality, eco-friendly product at a low price
How to use Balancing powder ®
Balancing Powder® is placed inside the tyre before this is fitted to the rim. At a speed of 30 km/t the centrifugal forces begin to take effect, whereupon the balancing powder is slung around in the tyre, and the balancing effect begins to occur. The vibrations that arise in the tyre’s contact with the roadway cause the balancing powder to move to the area of imbalance. This occurs constantly while driving, thus producing a dynamic balance.
Balancing Powder® is a brand new, dynamic and technically correct replacement for balancing weights that use lead or other metals.
It all began with aircraft safety
Balancing Powder® was originally developed in 1990 for aircraft landing wheels. It is a safe balancing technique, because the balancing powder is kept inside the tyre, thus replacing balancing weights which might fall off and damage the aircraft at take-off or landing.
Balancing Powder® has been further developed for use with buses, trucks, vans and even small cars.
Balancing Powder® is
- easy to use
- is placed inside the tyre without the use of balancing machines
- meets the future’s global environmental requirements – and the EU directive banning traditional lead balancing from 1 January 2008
- is a competitively-priced alternative to all known balancing techniques
- is hi-tech and high quality at a low price
- is the balancing powder with the highest specific gravity, thus ensuring optimum balancing – even at high speeds and in rapid turns
- is unaffected by moisture
- causes no wear on the inner liner and tyre carcase
- minimises wear and tear on tyres
- is simple to fi t and can be used with aluminium or steel rims tyres
Plastic Welding system
The best and most compleate plastic welding system from HBC system
HBC system offers this all-purpose, portable plastic welding kit for repairing tanks, tarps, liners, conveyor belts, automotive, truck, motorcycle and marine body parts as well as other thermoplastic products of all types.
The HBC Plastic Welding kit includes everything necessary in one tool box to make a professional quality thermoplastic repairs in the field and in the shop.
The welding system from HBC system is the most profesional sytem for high end plastic welding repairs
System B6 Plastic welding kit can be ordered onlin on this link
HBC system offers this all-purpose, portable plastic welding kit for repairing tanks, tarps, liners, conveyor belts, automotive, truck, motorcycle and marine body parts as well as other thermoplastic products of all types.
The HBC Plastic Welding kit includes everything necessary in one tool box to make a professional quality thermoplastic repairs in the field and in the shop.
The welding system from HBC system is the most profesional sytem for high end plastic welding repairs
System B6 Plastic welding kit can be ordered onlin on this link
Dashboard Repair
HBC system B1 is a system for repairs of plastic, leather & vinyl both hard and flexible as well as interior as exterior parts, bumpers, dashboards and leather & vinyl componentsSystem B1 contains a complete assortment of adhesives ranging from specially developed hotmelt with fine structure to soft, flexible, or hard bumper- adhesive for dash-boards and glass fibre boxes on
caravans and lorries.
The system is complete with cleansing fluids, primers, and reinforcement material. Included are all the required tools and adhesive materials to complete the repair from start to finish.
The system makes it possible to repair hard and flexible plastic, both interior and exterior parts, bumpers, dashboards, as well as leather and vinyl components.
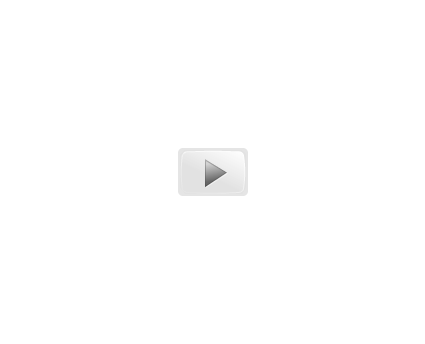
System B1 mini Mostly for Dashboards can be ordered online on this link
caravans and lorries.
The system is complete with cleansing fluids, primers, and reinforcement material. Included are all the required tools and adhesive materials to complete the repair from start to finish.
The system makes it possible to repair hard and flexible plastic, both interior and exterior parts, bumpers, dashboards, as well as leather and vinyl components.
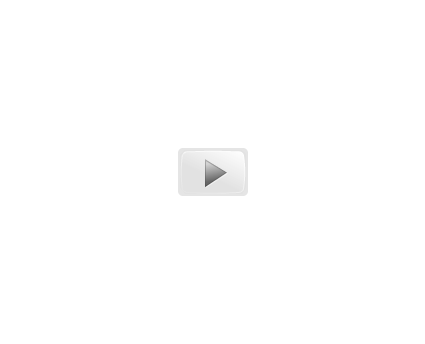
System B1 mini Mostly for Dashboards can be ordered online on this link
Thursday, January 26, 2012
Leather Repair
Dent removal step by step Manual system G
Manual System G
1. Introduction
Paintless dent removal is a craft, which only can be learned by following this instructional manual closely along with lots of training. Successful repairing of dents without repainting depends strongly on coordinating eye and hand. To develop this coordinating skill so that you quick and safe can remove dents, the manual must be followed and the training be done until you can carry this out correctly every time.
This manual contains eight sections:
1. Introduction
2. Tools
3. Hand tools
4. Dent terminology
5. Basic training
6. Basic dent beating out
7. Working with cars
8. Conclusion
The manual is carefully elaborated to guide you – step by step – through the procedure of beating out dents without after painting.
Some learn faster than others, so do not get impatient. Nobody has ever learned this working method overnight so be fair to your self and take the time you need.
2. Dent Removal Tools
The tools are the longer, heavier equipment in the kit. They are used for dents, which are located so that you have no access to them from the downside.
The tools are divided according to types and shapes of the working ends.
The tools are manufactured from polished or 4140 steel instead of stainless steel. Stainless steel is too soft, which makes it difficult to control the pressure during repairing of dents.
The points on the tools are developed and specified according to different properties in sheet metal. This development has taken place over a range of years to meet the need at people with great practical working experience within repairing. But people work in different ways and develop their own method of repairing; therefore we do not recommend specific which point to use at a given job.
As earlier said paintless dent removal is a craft, which relies on estimate and experience of the person doing the job. Some do almost all repair work with one type of point. Others may use two or three different points for one dent. Going through the training programme you will get the chance to try out different points and hereby gain the experience necessary in order to know every point. If you work better with one type for a certain dent, you can go ahead and use that one.
The five types of points are as follows:
Knife tool
Cutter tool
Ball tool
Blade tool
Tri-point tool
Knife tool
The bars on the knife tools bend and are shaped as a long wedge at the end. They have a sharp edge.
The knife tools are mostly used for repairing small dents – so called micro grooves – because of the dot on the end of the point. They are also useable for a certain kind of dents called ponds.
One of the best qualities of the knife tool is the way in which, it “catches” the metal. When it reaches the right spot it stays there.
Please notice that the greatest danger in using the knifepoint is, that it may scratch the metal if pushed to hard. Because scratches are the worst that can occur in repairing dents without after painting, you should be very careful in using the knife tool.
Cutter tool
The ends have two flat edges and one round top.
Billede
Cutter tools are good at finishing dents. They are very good in beating out doors and other vertical bodywork parts as they are very sharp and because they grab a hold of the metal surface.
Like the knife tool the cutter tools can also scratch the metal when pushed to hard, so please take care in using them
Ball tools
The ends are rounded in ball shape. The ball tool is a really good all-round tool.
Billede
As the ends are rounded, the ball tool behaves “softer” than the other ends. It is therefore possible to put more strength into the work. Many people think, that the ball tool is the easiest to control. It is good at removing lighter damages and small dents.
The potential danger in the ball tool lies in making an elevation – a reversed dent – and that it slips. The ball tool does not catch on to the metal so well as a knife or carving point, so you should be careful to hold the tool where you want it.
Blade tools
They have flat ends and a rounded top.
Billede
Blade tools are fine tools for all purposes, even though they are not as “soft” as ball tools.
Blade tools catches the metal pretty well from side to side, yet they have a tendency to slide back and forth; so please be careful keeping them under control.
The potential danger in the blade tool is the same as for the ball tool – to make an elevation.
Tri-point tool
The ends have 2 bendings; the point is tri-pointed with a rounded spot.
Billede
The tri-point tool is used for the work with the heavy, thick metal, which can be found on cars like Mercedes-Benz and BMW.
The tri-point tool is usually too heavy a tool for lightweight compact and semi-compact cars.
Because the tri-point tool is so stiff, it is easier to make an elevation with this tool than with the other tools, so move forward slowly, until you get in touch with the tool.
3. Hand tools
Hand tools are a shorter, thinner form of the tools, but do not underestimate them. Compared to the length, the hand tool is stronger than the other tools, so it is still relative easy to use a considerable amount of force on the dent.
The hand tool can be used either like the tools – as arms, using the side of the hole or another admission point as support – or with the point directly placed on the dent. Hand tools can first and foremost be used when working with dents close to the support of the roof, trucks and bonnet; they can, though, also sometimes be useful for doors, wings and rear skirting boards.
Even though the difference between many tools with the same type of point is the length, the tools are in some cases bended in different angles. The most usable bendings have been decided – after a long period of experience - in order to be able to reach the hardly accessible places. If it is impossible to reach a dent with the used tool, please try one of the hand tools with a different bending. You will be surprised, how easy it is to reach the dent. It may be so, that you have to try different tools before finding the right one, but eventually you will automatically find the right one immediately.
4. dent terminology
Billede fordybninger
Grooves are the most common dent and the one you most often work with. Car doors, shopping trolley, children and hail, cause the grooves.
Micro grooves are tiny. Sometimes they are a result from the dent beating out process.
Billede forhøjninger
Elevations are the opposite of grooves – they go outwards instead of inwards. Most elevations occur
when you remove a groove.
Micro elevations are tiny and occur in the dent beating out process.
Billede spidsforhøjning
A pointed elevation is nearly the worst that can happen to the bodywork. They are almost impossible to repair without repainting, even though they can be reduced.
The following dents have all occurred during beating out. Micro elevations and grooves are only a part of the work. The following dents have occurred as a result of mistakes.
Billede dam
A pond may occur when removing micro elevations. A pond is a low, flat spot that is wider than a micro groove.
billede Flade
A flat is an even, flat area on the bottom of a groove. If it were levelled with the rest of sheet metal, it would be okay but it is not. Flats occur usually when you start to work on a dent from the middle instead of from the edges.
Billede flimmer
Shimmer occurs when you have worked too much on a dent. The metal looses its flexibility and becomes stiff. This usually happens, when you have mended too many micro grooves and micro elevations, which lead to the metal crystallizing.
Most of these problem dents can be avoided by learning exactly where the tool point is, and use precisely the pressure necessary to mend the metal and remove the dent.
Therefore patience and training are so important in beating out dents without repainting.
Shimmer can also lie in clear paint, but can in many cases be helped by polishing with a grindstone grain 1500 – 2000 – 3000, along with after polishing.
5. Basic training
Before starting work on the customer’s cars you need a lot of practise. For that use you need a training bonnet.
The best place to find a bonnet is in a bodywork garage or at a car breaker. Bonnets need not have neither dents nor be in perfect condition.
It is important though, that the paint on the bonnet is in good condition. You should be able to polish the bonnet so the lamp gives good reflections. These light reflections must lead the work.
It is much easier to learn on the dark paint colours, as the dark colours show the defects better than light ones. Red, dark blue and black are all good choices.
Also in training a bonnet of light metal is easier to use than one of stronger metal. Try and find bonnets with the most possible space between the side members, as you will need the space for training.
Most likely, you need more than one bonnet before you are through. It takes a lot of practise to learn beating out of dents without repainting and most people need at least 2 bonnets, before they are ready for the customer’s car.
The only way you ever learn beating out dents without after painting, is by performing the training, which is a part of the training programme, and by keeping on training until you have learned.
FIRST TRAINING PART: Adjusting the light
This training part shows how the reflection from the lamp should look like. You must learn to adjust the light easy and quick in the right position, so that it reflects in the dent that is to be repaired. Draw a circle around the dent and adjust the light so that the reflections are within the circle before starting the work.
SECOND TRAINING PART: Reflections from the dent
In this training part you shall make some dents and then learn to find them by means of the light reflections. The different dents reflect the light in their own way. Until you automatically recognize the different ways in which, the light is reflected, you are not able to repair dents on the customers’ cars.
This is a diagram on a typical reflection of a groove:
Billede
The metal reflects the light from the pipes in a way that they look like curving around the dent.
This is a diagram on a typical reflection of an elevation:
Billede
The metal reflects the light from the pipes in a way that they look like being drawn against the dent. But these diagrams only give an assumption on the real picture.
THIRD TRAINING PART: Placing the tool point
The light shows the exact placement of tool or hand tool, and you must know this before pressing on the metal to bend it. Until you have learned this and learned it correctly, you cannot begin to repair dents.
FOURTH TRAINING PART: Circles
This training part is to develop accuracy in placing the tool point and press just so hard, that the metal moves. It is the first of three training parts, which gradually gets harder.
In this training you must make elevations in the middle of circles, which you draw on the bonnet.
FIFTH TRAINING PART: X’s
When you have gained a little accuracy in placing the tool point within a circle, you must continue with X’s. Try and place an elevation in the middle of each X.
SIXTH TRAINING PART: Points
When you can hit the middle of an X each time, you proceed to making elevations in the middle of a number of points. This is very difficult, so please do not get impatient and continue, until it can be done every time.
Most likely this will take a few days, maybe a week or more, before you have worked your way through all the training and can hit the middle of a number of points time after time. While you learn to place the tool point, you also develop the eye/hand coordination and you learn, how the tool should be handled with different strength, all at one time.
6. Basic dent beating out
Dent beating out without repainting is ways of getting the metal back in the shape it had, before the dent occurred. Sheet metal has a kind of “memory”, so what you should do is to push the metal carefully back to its original shape. As long as the metal has not been dented too long or too many times, the dent will react to your efforts.
Face of a clock method
The first impulse will probably be to take a tool with ballpoint and start to press at the middle. That is a bad idea and will probably result in a flat or division of the dent.
Instead it is advisable to use the so-called face of a clock method. Visualize the outline of a clock around the dent. The twelve o’clock is the point farthest away from you, when you shall work on the dent. When looking at the dent from above, it will resemble the drawing underneath. You are placed in the bottom of the drawing.
Billede urskive
You start by pressing at twelve o’clock, then 11, 1, 2, 10, 9, and 3. This makes the dent a little smaller. Start again at twelve o’clock, this time closer to the centre, as the dent is smaller now.
Remember to work from the outer edge of the damaged area. Do not get too fast to the centre. Stay in the upper half of the clock. It is not necessary to work on the dent’s lower half, as it automatically will follow the upper half.
Removal of grooves
First you polish the damaged baseboard. This makes it easier to se the damage. Training grooves can be made with a round hammer or the bar of a large screwdriver, protected by a couple of layers of fabric. Avoid damages over the side members. Form a circle around the damage. Start with a small dent, as you will experience, that a dent sized 10 mm will cause damage to an area sized 25 mm. Choose a tool long enough to reach the dent, without it reaching to far out of the baseboard. Let the tool slide through the “S”-hook and make sure, that you have a good working position, when the dent has been located.
REMOVE ELEVATIONS
Most elevations will be micro elevations, which have occurred by removal of grooves. It is therefore necessary also to be able to handle these. Elevations can be removed by knocking lightly on the surface. You should be very careful, so that the paint is not damaged. Protect the hammer or the mandrel with tape.
In beating out elevations, you are advised to use the same “face of a clock” method, but you need to work slowly and with careful knocks. Make sure, that the beating out is levelled with the metal and not under it. Use the light and look from all sides. Check often how the work progresses. Be careful that the angles do not get too sharp.
When you have practised on both grooves and elevations, and you feel confident in removing them, the time has come to start on cars. Only you can decide, when you are ready to begin.
7. Working with cars
It would be nice, if all dents were located on the bonnet from the training bench. But since they aren’t the time has come to move forward into the real world.
First and foremost you must know, that some dents can be taken care of immediately. Others require more experience, and then there are some dents, which probably never can be repaired perfectly.
It is important to know the characteristics of the different dents before deciding, how to handle these.
The depth and angle of the dent affects the firmness of the metal and also how difficult it will be to repair. The deeper the hole the sharper the angles, the more difficult the beating out will be.
Sharp elevations are the most difficult dents to work with, as the metal has been pushed to a peak. The sides are very steep and the metal is very stiff.
When you have gained a certain amount of experience, you will be able to diminish the sharp elevations, but that is probably not something you want to try, once you have just started.
In the beginning you will rather not take on beating out of dents on the outlines of the bodywork, as these have been punched or rolled on the factory. The process of making outlines hardens the metal and makes it very difficult to work with.
In spite of this, most dents can be fixed and you will probably find it no more difficult – but a lot more interesting- than working with training bonnets.
ACCESS
Dent located in different places on the car cause different problems and we will therefore go through these one by one. We will start with the easiest places: the bonnet, tail gate and the roof.
BONNETS
Even on the bonnet, you should not start beating out before you are absolutely sure, that you can reach the dent. The first you should do is of cause to open up the bonnet and see, what can be seen. On many cars it will be necessary to remove the insulation.
Look for dents close to the profiles on the hood. Often this area is reinforced double, and you cannot reach the bottom of the dent to do beating out with out after painting.
If the dent is above or close to a shore, you must be sure that the shore can be disengaged.
What you actually must do to disengage the shore, is to loosen the glue, which holds the shore to the metal. You need not glue again, when you have finished the work, because on the next coming hot day or the next time that the engine room is warmed up, the glue will stick the shore back on again.
If the dent is sited directly over a side member, it may be necessary to drill a hole in the side member, in order to get access to the dent. Remember to use a drill stop, and to tighten it so that it does not slide.
Exceptional, under the assumption that the dent is in the right place, the disengagement of the shore may cause the dent to pop out. As already mentioned, this happens very rarely, and you must never disengage the shore hoping that the dent pops into place.
The only exception is on the big flat dents, which some times occur, when leaning on the bonnet, the tail gate or the roof; or if you place something heavy on the car. In that case is the first thing you should do, is to try and disengage the shore.
BOOT
Tail gates can be a bigger problem than bonnets, because the curbs in the metal usually are sharp and because the tail gates have more shores.
Spoilers can also be a big problem, if the dent is too close to the bars. The bars throw a shadow and obscure part of the reflections you need at the beating out.
If the spoiler is screwed on, it is not a problem, then they can just be removed. But many spoilers are riveted on, so therefore you have to shine the light and work on the dent from at least two angles, and this takes longer.
Roof installed rails give the same problem and therefore must be solved in the same way.
ROOF
Before doing anything with the roof, you must remove the ceiling lining. It may look as if every car producer has its own way of installing the ceiling lining in the different models.
There are though some common features for all ceiling lining. It is necessary to remove sunshades, trim and ceiling light. Some ceiling linings will then fall down. Others may be glued on. You have to take one car at a time.
When the ceiling lining has been removed, the work with the roof is similar to the work on the bonnet, though now you can stand upright instead of bending over.
Sunroofs are a problem of their own. It will probably be necessary to dismantle the sunroof. Usually it is only bolted or screwed on, so it is rather easy.
But NEVER CARRY OUT THE WORK ALONE. You need somebody to hold the sunroof, while dismantling it. If you loosen the one side and the sunroof falls out, a sharp elevation, which is impossible to remove, will occur.
It is also necessary to be two people to install the sunroof again.
In some ways, mudguards, doors and skirting boards are easier, because they have vertical surfaces. Therefore many people feel that these are easier to work with.
When you beat out dents on vertical surfaces, the light must be set in a vertical position. The lamp must of cause first be moved away from the car that you work on. Then the lamp shall be swung head up over the top and lowered down slowly, until it is resting on the buttress.
Usually it will be necessary to look closely to beat out dents on vertical surfaces, but usually there are many ways in which to get to the dent.
MUDGUARD
It will always be an advantage if you can get to the dent through the headlight or the flasher. Remove the container and use the opening sides as support.
It may be necessary to go through the door hinge panel, if you can find an opening to the mudguard, but use only the hinge panel if there is no other option.
There may be cases in which, it is best to drill through the engine room. In cases where the dent is on the top of a mudguard, or if you cannot get in the other way.
If it will be necessary to drill, there must be held a reasonable distance from point weldings or rivets. Some prefer to drill frontal, just behind the dent and mend the dent with hand tools. Others prefer to continue the hole and use the side of the hole to render support to the bar or one of the large hand tools.
Whether you drill in a door, a mudguard or a panel, you should always be careful to tighten the holes with rubber bodywork stoppers, when you have finished. Use for safety’s sake always a little tightening mass on the stopper.
Do also remember, that if a dent has damaged a designer line, it may not be possible to repair 100%.
REAR END PANEL
Panels look like mudguards, except that the best access possibility is through the taillight. Sometimes the best access is through the doorpost. Look after what is behind all stoppers, and do not hesitate to remove the ventilation grill, if there is one. This can be a good starting point.
Another fine access to some dents is through the fuel filling pipe stub. It will probably be necessary to drill, so do remember to close holes afterwards with a rubber stopper. It is especially important to use adhesive in this area, as the lid often is opened and the stopper can be worn.
When the dent is located on a quarter panel, the best working method is sometimes through the boot. You can often hang a S-hook on the edge of the boot to support the bar. Please take care, that the weather strip is not damaged.
DOORS
When you beat out dents with out after painting on a door, the first you should do is to close the window.
Check out the door edges for stoppers. Remove those that are there and examine what is behind them. Some car producers, for example Honda, have original holes in the doors, so that it will be easier to repair possible minor damages occurred during delivery. If it turns out that there only is the window adjustment or similar behind the stopper, then close again and keep looking. Look for a ventilation grill and get access through that.
Every time you must work on a door, it must be secured in the working position with the door lock, before even doing anything more than removing a stopper. And especially before starting to drill. Never trust that the door stop can hold the door tight, while you work.
8. Conclusion
No matter where the dent is placed, you are going to need all that you have learned, once you decide how to get to it:
· First polish the working surface, so that the best light reflection can be obtained.
· Use the light to “read” the dent and to tell exactly, where the tool point is located, before pressing on the tool to correct the metal.
· Use the “face of a clock” method on the dent, so that the sides of the dent are bend against the centre.
· Be patient. Take the time that is necessary. In the long run, slowly is quick.
· When you remove elevations, use 10-15 small knocks instead of one hard knock.
· Be extra careful with the knife tools and the cutter tool, as they can scratch the metal. Instead use for example a hammer handle.
1. Introduction
Paintless dent removal is a craft, which only can be learned by following this instructional manual closely along with lots of training. Successful repairing of dents without repainting depends strongly on coordinating eye and hand. To develop this coordinating skill so that you quick and safe can remove dents, the manual must be followed and the training be done until you can carry this out correctly every time.
This manual contains eight sections:
1. Introduction
2. Tools
3. Hand tools
4. Dent terminology
5. Basic training
6. Basic dent beating out
7. Working with cars
8. Conclusion
The manual is carefully elaborated to guide you – step by step – through the procedure of beating out dents without after painting.
Some learn faster than others, so do not get impatient. Nobody has ever learned this working method overnight so be fair to your self and take the time you need.
2. Dent Removal Tools
The tools are the longer, heavier equipment in the kit. They are used for dents, which are located so that you have no access to them from the downside.
The tools are divided according to types and shapes of the working ends.
The tools are manufactured from polished or 4140 steel instead of stainless steel. Stainless steel is too soft, which makes it difficult to control the pressure during repairing of dents.
The points on the tools are developed and specified according to different properties in sheet metal. This development has taken place over a range of years to meet the need at people with great practical working experience within repairing. But people work in different ways and develop their own method of repairing; therefore we do not recommend specific which point to use at a given job.
As earlier said paintless dent removal is a craft, which relies on estimate and experience of the person doing the job. Some do almost all repair work with one type of point. Others may use two or three different points for one dent. Going through the training programme you will get the chance to try out different points and hereby gain the experience necessary in order to know every point. If you work better with one type for a certain dent, you can go ahead and use that one.
The five types of points are as follows:
Knife tool
Cutter tool
Ball tool
Blade tool
Tri-point tool
Knife tool
The bars on the knife tools bend and are shaped as a long wedge at the end. They have a sharp edge.
The knife tools are mostly used for repairing small dents – so called micro grooves – because of the dot on the end of the point. They are also useable for a certain kind of dents called ponds.
One of the best qualities of the knife tool is the way in which, it “catches” the metal. When it reaches the right spot it stays there.
Please notice that the greatest danger in using the knifepoint is, that it may scratch the metal if pushed to hard. Because scratches are the worst that can occur in repairing dents without after painting, you should be very careful in using the knife tool.
Cutter tool
The ends have two flat edges and one round top.
Billede
Cutter tools are good at finishing dents. They are very good in beating out doors and other vertical bodywork parts as they are very sharp and because they grab a hold of the metal surface.
Like the knife tool the cutter tools can also scratch the metal when pushed to hard, so please take care in using them
Ball tools
The ends are rounded in ball shape. The ball tool is a really good all-round tool.
Billede
As the ends are rounded, the ball tool behaves “softer” than the other ends. It is therefore possible to put more strength into the work. Many people think, that the ball tool is the easiest to control. It is good at removing lighter damages and small dents.
The potential danger in the ball tool lies in making an elevation – a reversed dent – and that it slips. The ball tool does not catch on to the metal so well as a knife or carving point, so you should be careful to hold the tool where you want it.
Blade tools
They have flat ends and a rounded top.
Billede
Blade tools are fine tools for all purposes, even though they are not as “soft” as ball tools.
Blade tools catches the metal pretty well from side to side, yet they have a tendency to slide back and forth; so please be careful keeping them under control.
The potential danger in the blade tool is the same as for the ball tool – to make an elevation.
Tri-point tool
The ends have 2 bendings; the point is tri-pointed with a rounded spot.
Billede
The tri-point tool is used for the work with the heavy, thick metal, which can be found on cars like Mercedes-Benz and BMW.
The tri-point tool is usually too heavy a tool for lightweight compact and semi-compact cars.
Because the tri-point tool is so stiff, it is easier to make an elevation with this tool than with the other tools, so move forward slowly, until you get in touch with the tool.
3. Hand tools
Hand tools are a shorter, thinner form of the tools, but do not underestimate them. Compared to the length, the hand tool is stronger than the other tools, so it is still relative easy to use a considerable amount of force on the dent.
The hand tool can be used either like the tools – as arms, using the side of the hole or another admission point as support – or with the point directly placed on the dent. Hand tools can first and foremost be used when working with dents close to the support of the roof, trucks and bonnet; they can, though, also sometimes be useful for doors, wings and rear skirting boards.
Even though the difference between many tools with the same type of point is the length, the tools are in some cases bended in different angles. The most usable bendings have been decided – after a long period of experience - in order to be able to reach the hardly accessible places. If it is impossible to reach a dent with the used tool, please try one of the hand tools with a different bending. You will be surprised, how easy it is to reach the dent. It may be so, that you have to try different tools before finding the right one, but eventually you will automatically find the right one immediately.
4. dent terminology
Billede fordybninger
Grooves are the most common dent and the one you most often work with. Car doors, shopping trolley, children and hail, cause the grooves.
Micro grooves are tiny. Sometimes they are a result from the dent beating out process.
Billede forhøjninger
Elevations are the opposite of grooves – they go outwards instead of inwards. Most elevations occur
when you remove a groove.
Micro elevations are tiny and occur in the dent beating out process.
Billede spidsforhøjning
A pointed elevation is nearly the worst that can happen to the bodywork. They are almost impossible to repair without repainting, even though they can be reduced.
The following dents have all occurred during beating out. Micro elevations and grooves are only a part of the work. The following dents have occurred as a result of mistakes.
Billede dam
A pond may occur when removing micro elevations. A pond is a low, flat spot that is wider than a micro groove.
billede Flade
A flat is an even, flat area on the bottom of a groove. If it were levelled with the rest of sheet metal, it would be okay but it is not. Flats occur usually when you start to work on a dent from the middle instead of from the edges.
Billede flimmer
Shimmer occurs when you have worked too much on a dent. The metal looses its flexibility and becomes stiff. This usually happens, when you have mended too many micro grooves and micro elevations, which lead to the metal crystallizing.
Most of these problem dents can be avoided by learning exactly where the tool point is, and use precisely the pressure necessary to mend the metal and remove the dent.
Therefore patience and training are so important in beating out dents without repainting.
Shimmer can also lie in clear paint, but can in many cases be helped by polishing with a grindstone grain 1500 – 2000 – 3000, along with after polishing.
5. Basic training
Before starting work on the customer’s cars you need a lot of practise. For that use you need a training bonnet.
The best place to find a bonnet is in a bodywork garage or at a car breaker. Bonnets need not have neither dents nor be in perfect condition.
It is important though, that the paint on the bonnet is in good condition. You should be able to polish the bonnet so the lamp gives good reflections. These light reflections must lead the work.
It is much easier to learn on the dark paint colours, as the dark colours show the defects better than light ones. Red, dark blue and black are all good choices.
Also in training a bonnet of light metal is easier to use than one of stronger metal. Try and find bonnets with the most possible space between the side members, as you will need the space for training.
Most likely, you need more than one bonnet before you are through. It takes a lot of practise to learn beating out of dents without repainting and most people need at least 2 bonnets, before they are ready for the customer’s car.
The only way you ever learn beating out dents without after painting, is by performing the training, which is a part of the training programme, and by keeping on training until you have learned.
FIRST TRAINING PART: Adjusting the light
This training part shows how the reflection from the lamp should look like. You must learn to adjust the light easy and quick in the right position, so that it reflects in the dent that is to be repaired. Draw a circle around the dent and adjust the light so that the reflections are within the circle before starting the work.
SECOND TRAINING PART: Reflections from the dent
In this training part you shall make some dents and then learn to find them by means of the light reflections. The different dents reflect the light in their own way. Until you automatically recognize the different ways in which, the light is reflected, you are not able to repair dents on the customers’ cars.
This is a diagram on a typical reflection of a groove:
Billede
The metal reflects the light from the pipes in a way that they look like curving around the dent.
This is a diagram on a typical reflection of an elevation:
Billede
The metal reflects the light from the pipes in a way that they look like being drawn against the dent. But these diagrams only give an assumption on the real picture.
THIRD TRAINING PART: Placing the tool point
The light shows the exact placement of tool or hand tool, and you must know this before pressing on the metal to bend it. Until you have learned this and learned it correctly, you cannot begin to repair dents.
FOURTH TRAINING PART: Circles
This training part is to develop accuracy in placing the tool point and press just so hard, that the metal moves. It is the first of three training parts, which gradually gets harder.
In this training you must make elevations in the middle of circles, which you draw on the bonnet.
FIFTH TRAINING PART: X’s
When you have gained a little accuracy in placing the tool point within a circle, you must continue with X’s. Try and place an elevation in the middle of each X.
SIXTH TRAINING PART: Points
When you can hit the middle of an X each time, you proceed to making elevations in the middle of a number of points. This is very difficult, so please do not get impatient and continue, until it can be done every time.
Most likely this will take a few days, maybe a week or more, before you have worked your way through all the training and can hit the middle of a number of points time after time. While you learn to place the tool point, you also develop the eye/hand coordination and you learn, how the tool should be handled with different strength, all at one time.
6. Basic dent beating out
Dent beating out without repainting is ways of getting the metal back in the shape it had, before the dent occurred. Sheet metal has a kind of “memory”, so what you should do is to push the metal carefully back to its original shape. As long as the metal has not been dented too long or too many times, the dent will react to your efforts.
Face of a clock method
The first impulse will probably be to take a tool with ballpoint and start to press at the middle. That is a bad idea and will probably result in a flat or division of the dent.
Instead it is advisable to use the so-called face of a clock method. Visualize the outline of a clock around the dent. The twelve o’clock is the point farthest away from you, when you shall work on the dent. When looking at the dent from above, it will resemble the drawing underneath. You are placed in the bottom of the drawing.
Billede urskive
You start by pressing at twelve o’clock, then 11, 1, 2, 10, 9, and 3. This makes the dent a little smaller. Start again at twelve o’clock, this time closer to the centre, as the dent is smaller now.
Remember to work from the outer edge of the damaged area. Do not get too fast to the centre. Stay in the upper half of the clock. It is not necessary to work on the dent’s lower half, as it automatically will follow the upper half.
Removal of grooves
First you polish the damaged baseboard. This makes it easier to se the damage. Training grooves can be made with a round hammer or the bar of a large screwdriver, protected by a couple of layers of fabric. Avoid damages over the side members. Form a circle around the damage. Start with a small dent, as you will experience, that a dent sized 10 mm will cause damage to an area sized 25 mm. Choose a tool long enough to reach the dent, without it reaching to far out of the baseboard. Let the tool slide through the “S”-hook and make sure, that you have a good working position, when the dent has been located.
REMOVE ELEVATIONS
Most elevations will be micro elevations, which have occurred by removal of grooves. It is therefore necessary also to be able to handle these. Elevations can be removed by knocking lightly on the surface. You should be very careful, so that the paint is not damaged. Protect the hammer or the mandrel with tape.
In beating out elevations, you are advised to use the same “face of a clock” method, but you need to work slowly and with careful knocks. Make sure, that the beating out is levelled with the metal and not under it. Use the light and look from all sides. Check often how the work progresses. Be careful that the angles do not get too sharp.
When you have practised on both grooves and elevations, and you feel confident in removing them, the time has come to start on cars. Only you can decide, when you are ready to begin.
7. Working with cars
It would be nice, if all dents were located on the bonnet from the training bench. But since they aren’t the time has come to move forward into the real world.
First and foremost you must know, that some dents can be taken care of immediately. Others require more experience, and then there are some dents, which probably never can be repaired perfectly.
It is important to know the characteristics of the different dents before deciding, how to handle these.
The depth and angle of the dent affects the firmness of the metal and also how difficult it will be to repair. The deeper the hole the sharper the angles, the more difficult the beating out will be.
Sharp elevations are the most difficult dents to work with, as the metal has been pushed to a peak. The sides are very steep and the metal is very stiff.
When you have gained a certain amount of experience, you will be able to diminish the sharp elevations, but that is probably not something you want to try, once you have just started.
In the beginning you will rather not take on beating out of dents on the outlines of the bodywork, as these have been punched or rolled on the factory. The process of making outlines hardens the metal and makes it very difficult to work with.
In spite of this, most dents can be fixed and you will probably find it no more difficult – but a lot more interesting- than working with training bonnets.
ACCESS
Dent located in different places on the car cause different problems and we will therefore go through these one by one. We will start with the easiest places: the bonnet, tail gate and the roof.
BONNETS
Even on the bonnet, you should not start beating out before you are absolutely sure, that you can reach the dent. The first you should do is of cause to open up the bonnet and see, what can be seen. On many cars it will be necessary to remove the insulation.
Look for dents close to the profiles on the hood. Often this area is reinforced double, and you cannot reach the bottom of the dent to do beating out with out after painting.
If the dent is above or close to a shore, you must be sure that the shore can be disengaged.
What you actually must do to disengage the shore, is to loosen the glue, which holds the shore to the metal. You need not glue again, when you have finished the work, because on the next coming hot day or the next time that the engine room is warmed up, the glue will stick the shore back on again.
If the dent is sited directly over a side member, it may be necessary to drill a hole in the side member, in order to get access to the dent. Remember to use a drill stop, and to tighten it so that it does not slide.
Exceptional, under the assumption that the dent is in the right place, the disengagement of the shore may cause the dent to pop out. As already mentioned, this happens very rarely, and you must never disengage the shore hoping that the dent pops into place.
The only exception is on the big flat dents, which some times occur, when leaning on the bonnet, the tail gate or the roof; or if you place something heavy on the car. In that case is the first thing you should do, is to try and disengage the shore.
BOOT
Tail gates can be a bigger problem than bonnets, because the curbs in the metal usually are sharp and because the tail gates have more shores.
Spoilers can also be a big problem, if the dent is too close to the bars. The bars throw a shadow and obscure part of the reflections you need at the beating out.
If the spoiler is screwed on, it is not a problem, then they can just be removed. But many spoilers are riveted on, so therefore you have to shine the light and work on the dent from at least two angles, and this takes longer.
Roof installed rails give the same problem and therefore must be solved in the same way.
ROOF
Before doing anything with the roof, you must remove the ceiling lining. It may look as if every car producer has its own way of installing the ceiling lining in the different models.
There are though some common features for all ceiling lining. It is necessary to remove sunshades, trim and ceiling light. Some ceiling linings will then fall down. Others may be glued on. You have to take one car at a time.
When the ceiling lining has been removed, the work with the roof is similar to the work on the bonnet, though now you can stand upright instead of bending over.
Sunroofs are a problem of their own. It will probably be necessary to dismantle the sunroof. Usually it is only bolted or screwed on, so it is rather easy.
But NEVER CARRY OUT THE WORK ALONE. You need somebody to hold the sunroof, while dismantling it. If you loosen the one side and the sunroof falls out, a sharp elevation, which is impossible to remove, will occur.
It is also necessary to be two people to install the sunroof again.
In some ways, mudguards, doors and skirting boards are easier, because they have vertical surfaces. Therefore many people feel that these are easier to work with.
When you beat out dents on vertical surfaces, the light must be set in a vertical position. The lamp must of cause first be moved away from the car that you work on. Then the lamp shall be swung head up over the top and lowered down slowly, until it is resting on the buttress.
Usually it will be necessary to look closely to beat out dents on vertical surfaces, but usually there are many ways in which to get to the dent.
MUDGUARD
It will always be an advantage if you can get to the dent through the headlight or the flasher. Remove the container and use the opening sides as support.
It may be necessary to go through the door hinge panel, if you can find an opening to the mudguard, but use only the hinge panel if there is no other option.
There may be cases in which, it is best to drill through the engine room. In cases where the dent is on the top of a mudguard, or if you cannot get in the other way.
If it will be necessary to drill, there must be held a reasonable distance from point weldings or rivets. Some prefer to drill frontal, just behind the dent and mend the dent with hand tools. Others prefer to continue the hole and use the side of the hole to render support to the bar or one of the large hand tools.
Whether you drill in a door, a mudguard or a panel, you should always be careful to tighten the holes with rubber bodywork stoppers, when you have finished. Use for safety’s sake always a little tightening mass on the stopper.
Do also remember, that if a dent has damaged a designer line, it may not be possible to repair 100%.
REAR END PANEL
Panels look like mudguards, except that the best access possibility is through the taillight. Sometimes the best access is through the doorpost. Look after what is behind all stoppers, and do not hesitate to remove the ventilation grill, if there is one. This can be a good starting point.
Another fine access to some dents is through the fuel filling pipe stub. It will probably be necessary to drill, so do remember to close holes afterwards with a rubber stopper. It is especially important to use adhesive in this area, as the lid often is opened and the stopper can be worn.
When the dent is located on a quarter panel, the best working method is sometimes through the boot. You can often hang a S-hook on the edge of the boot to support the bar. Please take care, that the weather strip is not damaged.
DOORS
When you beat out dents with out after painting on a door, the first you should do is to close the window.
Check out the door edges for stoppers. Remove those that are there and examine what is behind them. Some car producers, for example Honda, have original holes in the doors, so that it will be easier to repair possible minor damages occurred during delivery. If it turns out that there only is the window adjustment or similar behind the stopper, then close again and keep looking. Look for a ventilation grill and get access through that.
Every time you must work on a door, it must be secured in the working position with the door lock, before even doing anything more than removing a stopper. And especially before starting to drill. Never trust that the door stop can hold the door tight, while you work.
8. Conclusion
No matter where the dent is placed, you are going to need all that you have learned, once you decide how to get to it:
· First polish the working surface, so that the best light reflection can be obtained.
· Use the light to “read” the dent and to tell exactly, where the tool point is located, before pressing on the tool to correct the metal.
· Use the “face of a clock” method on the dent, so that the sides of the dent are bend against the centre.
· Be patient. Take the time that is necessary. In the long run, slowly is quick.
· When you remove elevations, use 10-15 small knocks instead of one hard knock.
· Be extra careful with the knife tools and the cutter tool, as they can scratch the metal. Instead use for example a hammer handle.
Order Procedure
The HBC products are marketed through local national HBC partners, who act as marketing, and distribution channels for systems, consumables, technical training, and marketing. Being IATA certificated, HBC system is also allowed to ship dangerous goods across the world.
If you are intersted in buying our systems please contact us to get an offer or find out if there is a local distributor in your area.
Your HBC contact persons are as mentioned below and can be contacted via:
Email: info@hbc-system.com
Manager of finance Vibeke Jorgensen (Orders, invoices etc.)
Sales Assistant Cecilia Brun Jensen (Shipping, claims (orders)
Marketing Manager Jan Hovgaard (web, print, marketing materials)
Key Account Manager Mette Andersen (Prices and PA to Henrik Bro)
Senior Training Manager John Speet (Technical support)
If you are intersted in buying our systems please contact us to get an offer or find out if there is a local distributor in your area.
Your HBC contact persons are as mentioned below and can be contacted via:
Email: info@hbc-system.com
Phone: +4570227070
Please address your request to the person responsible:
President/CEO Henrik Bro Christensen
Manager of finance Vibeke Jorgensen (Orders, invoices etc.)
Sales Assistant Cecilia Brun Jensen (Shipping, claims (orders)
Marketing Manager Jan Hovgaard (web, print, marketing materials)
Key Account Manager Mette Andersen (Prices and PA to Henrik Bro)
Senior Training Manager John Speet (Technical support)
HBC System E complete; Caravan repair training
HBC System E complete; Caravan repair
According to insurance companies about 60% of all damaged side panels of caravans and mobile homes can be repaired instead of replaced. The savings by repairing instead of replacing this side panel can be more than 70%, not even mentioning the problems of moisture after replacing the side panels. The patented repair method of HBC system E, which creates a structure copy of the original pattern and uses an unique injection method of the filler, allows you to do repairs up to 3 meters! The repair of the damage must be conducted in a professional way. The 2 days Caravan training will be sufficient to give you a solid basis to do the repair in a professional way.
PurposeAt the end of this course you will be able to repair structured panels on caravans and mobile homes.
Intented for:
(Employees of) bodyshops, caravan – mobile home repair companies, caravan – mobile home dealers, caravan – mobile home rental companies, etc.
Process The course is divided into a theoretical and practical part. Each participant will have the opportunity to practise the repair methodes on various materials and structures. It is possible during the training to work with the repair kit, you use in your company. This implies of course that you bring this repair kit to the course.
Test
At the end of the course you will have to pass a test. This test is a practical test, where you will have to do a repair on a caravan - mobile home panel.
Certificate
When you passed the test positively you will receive a certificate.
Duration:
1-2 days
Program
· Introduction of HBC system E; caravan repair
· Explanation internet; where to find manuals, step-by-step charts, video, order forms, etc.
· Explanation of the tools in the system
· Explanation of the consumables in the system
· Run video HBC system DVD
· Theory about the usage of the tools in the system
· Theory about the repeating structure; fine, coarse and flat panels
· Theory about the repair of holes in caravan panels
· Theory about the making of the mould, filling of the dent and painting the damage
· Demonstration of the caravan repair system
· Exercises with the caravan repair system
· Selecting the right colour, using the colour selector
· Explanation of HBC system caravan spotrepair
· Explanation of the software with Mixing Formulas
· Mixing the colour, using the software
· Colouring the repair
· Tips and tricks, how-to-sell
· Test
· Evaluation
Needed systems· HBC System E complete
· HBC system Caravan spotrepair
· Sanding paper P240-P400-P1200-Scotch brite (grey)
· Clean cloths
· Compressor
· Heat gun
Needed training material
· Caravan panels with structure
http://www.hbc-system.com/Dent-repair-system-for-caravans-5163.aspx
According to insurance companies about 60% of all damaged side panels of caravans and mobile homes can be repaired instead of replaced. The savings by repairing instead of replacing this side panel can be more than 70%, not even mentioning the problems of moisture after replacing the side panels. The patented repair method of HBC system E, which creates a structure copy of the original pattern and uses an unique injection method of the filler, allows you to do repairs up to 3 meters! The repair of the damage must be conducted in a professional way. The 2 days Caravan training will be sufficient to give you a solid basis to do the repair in a professional way.
PurposeAt the end of this course you will be able to repair structured panels on caravans and mobile homes.
Intented for:
(Employees of) bodyshops, caravan – mobile home repair companies, caravan – mobile home dealers, caravan – mobile home rental companies, etc.
Process The course is divided into a theoretical and practical part. Each participant will have the opportunity to practise the repair methodes on various materials and structures. It is possible during the training to work with the repair kit, you use in your company. This implies of course that you bring this repair kit to the course.
Test
At the end of the course you will have to pass a test. This test is a practical test, where you will have to do a repair on a caravan - mobile home panel.
Certificate
When you passed the test positively you will receive a certificate.
Duration:
1-2 days
Program
· Introduction of HBC system E; caravan repair
· Explanation internet; where to find manuals, step-by-step charts, video, order forms, etc.
· Explanation of the tools in the system
· Explanation of the consumables in the system
· Run video HBC system DVD
· Theory about the usage of the tools in the system
· Theory about the repeating structure; fine, coarse and flat panels
· Theory about the repair of holes in caravan panels
· Theory about the making of the mould, filling of the dent and painting the damage
· Demonstration of the caravan repair system
· Exercises with the caravan repair system
· Selecting the right colour, using the colour selector
· Explanation of HBC system caravan spotrepair
· Explanation of the software with Mixing Formulas
· Mixing the colour, using the software
· Colouring the repair
· Tips and tricks, how-to-sell
· Test
· Evaluation
Needed systems· HBC System E complete
· HBC system Caravan spotrepair
· Sanding paper P240-P400-P1200-Scotch brite (grey)
· Clean cloths
· Compressor
· Heat gun
Needed training material
· Caravan panels with structure
http://www.hbc-system.com/Dent-repair-system-for-caravans-5163.aspx
Leather care system
The leather care kit from HBC system maintains the original, natural non-shiny leather sheen
This unique leather care system provides your with an original, natural satin sheen leather surface without leaving a greasy film residue. Slipping around at the leather seat is history - the leather protection cream leaves a mat non-greasy finish. The leather care products are suitable for leather seats, dashboards, stearing wheels etc.
The professional high performance leather care kit contains:

HBC INK REMOVER, STICK
Part no. 00.939, 20g
HBC Ink Remover eliminates stains and pen marks, ink and lipstick from pigmented leather. Do not use on nubuck, suede or aniline leather.
Instructions for use:
HBC LEATHER CLEANER, STRONG
Part no. 00.942, 250ml.
HBC Leather Cleaner, strong contains a highly effective detergent for cleaning pigmented leather upholstery like car, motorcycle, boat, airplane and sofa seats. It can also be used on other resistant leather articles like shoes and handbags. It is not suitable for aniline leathers, nubuck or suede. If you have a delicate skin or if you use frequently HBC Leather Cleaner, strong, please wear latex gloves while using the product.
Instructions for use:
HBC LEATHER GUARD (LEATHER PROTECTION CREAM) Part no. 00.941, 250ml.
HBC Leather Guard is a water based protection cream for all leather types, except nubuck and suede. HBC Leather Guard protects against oil, water and alcohol based stains as well as everyday dirt and grime. It will also keep your leather lovely and soft, and when used regularly prevents pigmented leather from cracking.
HBC STAIN REMOVER
Part no. 00.942, 250ml.
HBC Stain remover removes resistant stains from leather and PVC. Do not use on aniline, nubuck or suede. Use this product with caution.
Instructions for use:
The Leather Care System can be ordered here
HBC INK REMOVER, STICK
Part no. 00.939, 20g
HBC Ink Remover eliminates stains and pen marks, ink and lipstick from pigmented leather. Do not use on nubuck, suede or aniline leather.
Instructions for use:
- Remove the screw cap and push up the tip about 4 mm out of the tube, unscrewing it.
- Pre-test on a concealed area.
- Pass the HBC Ink Remover stick repeatedly over the point to be cleaned, pressing gently.
- Let the product work on the stain for about 30 seconds.
- Wipe off HBC Ink Remover with a soft dry cloth.
- Clean with Leather Cleaner.
- Apply HBC Leather Guard, rubbing the leather gently with circular movements, then let it dry.
Part no. 00.942, 250ml.
HBC Leather Cleaner, strong contains a highly effective detergent for cleaning pigmented leather upholstery like car, motorcycle, boat, airplane and sofa seats. It can also be used on other resistant leather articles like shoes and handbags. It is not suitable for aniline leathers, nubuck or suede. If you have a delicate skin or if you use frequently HBC Leather Cleaner, strong, please wear latex gloves while using the product.
- Shake the bottle well before using.
- Pre-test the colorfastness on a hidden area.
- Put HBC Leather Cleaner, strong onto a soft sponge and produce foam by squeezing it repeatedly.
- Clean the area without rubbing.
- Wipe the excess foam and the soiling away with a soft white cotton cloth.
- Dry with a dry cloth and let dry fully.
HBC Leather Guard is a water based protection cream for all leather types, except nubuck and suede. HBC Leather Guard protects against oil, water and alcohol based stains as well as everyday dirt and grime. It will also keep your leather lovely and soft, and when used regularly prevents pigmented leather from cracking.
We recommend your leather is cleaned and re-protected at least every six months. Aniline leather placed in rooms subject to heavier use may need cleaning more regularly and more thoroughly.
Instructions for use:
- Shake the bottle well before use.
- Pre-test on a concealed area.
- Put a small amount of HBC Leather Guard onto a soft, clean cloth and apply to the surface of the leather evenly. Repeat on areas subject to heavy use.
- Leave about 30 minutes to dry.
- Buff the leather lightly with a clean soft cloth.
Part no. 00.942, 250ml.
HBC Stain remover removes resistant stains from leather and PVC. Do not use on aniline, nubuck or suede. Use this product with caution.
Instructions for use:
- Apply a little HBC Stain remover on a clean cloth.
- Test the colour resistance of the leather on a hidden spot.
- Rub lightly on the leather to see if there is no colour transfer onto the cloth.
- If this test is OK, rub lightly with the cloth over the stained area.
- If needed, treat the stained area once more, checking regularly that no colour is transferred onto the cloth.
- Clean the treated area with HBC Leather Cleaner.
- Let dry and apply HBC Leather Guard
The Leather Care System can be ordered here
Slide hammer system – Step by step repair manual
Slide hammer system – Step by step repair manual
· Clean the repair area on the car with cleaner.
· Start the glue melting heat gun part no. 13.977 (ready after 2 minutes)
· To choose the right hot melt glue sticks:
Part no. Colour Temperature
o 13.975 Yellow 12-25 degrees, lower temperature.
o 13.976 Blue 15-40 degrees.
o 13.979 Black 12-25 degrees, lower temperature
*Right glue sticks depending of the humanity and temperature.
· The air humanity can make it difficult to advice exact temperature for the glue sticks.
· Place the Glue stick in the started heat gun.
· Pickup the right red Plastic top
o (small, medium, large).
o Best success if the plastic top and dent are similar size.
· Ad the melted glue on the plastic top -then fast place the plastic top in the central area of the dent.
o Place the plastic top in the deepest area of the dent
o Make sure the plastic top is stable and 90 degrees on the repair area.
- · Wait 3-4 minutes. The glue has to be cold.
- · Place the Slide hammer in the top set and pull the dent up in right level with small steps.
- · Remove the glue with Glue Remover
- · Polish the repair after finishing.
Important:
· Repeat the repair process if needed.
· If the dent by an accident is too high knock down the top with a nylon tip.
· The temperature and the air humanity make the glue stick works differently.
Accessories to slide hammer system
13.990 Slide hammer
14.009 Glue remover 100ml.
13.975 Glue sticks yellow 15pcs.
13.976 Glue sticks blue 15pcs.
13.979 Glue sticks black 15pcs.
446-447-448 Knock down punch
13.991 Rubber hammer
14.003 Blue Tips plastic set Alu tips
14.0031 Round 16mm. 1405 Round 15mm
14.0032 Round 20mm. 1406 Round 20mm
14.0033 Round 32mm. 1407 Round 25mm
14.0034 Round 40mm. 1408 Round 30mm
14.0035 Oval 50x30mm.
13.974 TIDY Tips plastic set 14.002 Orange thin soft plastic set
Round 15mm. 14.0021 Round 30mm.
Round 20mm. 14.0022 Round 40mm.
Round 25mm. 14.0023 Oval 50x30mm.
Ozone air cleaning manual
HBC System H - Car cleaner User manual
Following has to be considered before using
· Be sure that no persons or pets are in the car
· Be sure that the smelling source is removed
· Be sure that the car is standing in a well ventilated room or standing outside.
1. Place the machine in the centre of the cabin on a plain support.
2. Open one window approximately 3 cm
3. Start the fan in the car Without engine running
4. Connect the machine to the power supply
5. Adjust the timer between 0 – 60 minute (Normal 30 minute )
6. Close doors
7. Turn on the machine
8. Wait for the adjusted minutes
9. Turn off the fan in the car
10. Open doors and let the car be ventilated for 10 minutes or more
11. Now your car is odour free inside and the fan system is sterilised.
If the car is still not odour free because of the load of bad smelling you have to make one more treatment and follow point 1 – 11 again.
Now you can enjoy a clean fresh and sterilised car without the danger of infection from germs.
HBC system hope you will find this product satisfactory.
Headlight Repair System manual
Date of revision : 25-09-2011
Product trade name(s) Headlight Repair System
Product group : D
Part number(s) : 00.609
Expire date : Storage life: 6 months
Content :
Part no. 00.609-1: 250 ml clearcoat
Part no. 00.609-2: 125 ml activator
Part no. 00.609-3: 125 ml catalyst
Abrasives: P400 (2 discs ø75mm),
P600 (4 sky blue sheets 130x85 mm),
P800 4 Lemon sheets 130x85 mm),
P1500 (4 orange sheets 130x85 mm),
Polishing cloth
Typical Properties
Color / Grade of Gloss Transparent and colourless
Characteristics
Special three-component finish with excellent characteristics of resistance and adherence to polycarbonate- base plastic materials, such as lenses for vehicle lights, synthetic glazing ( as long as it is made of polycarbonate), yacht components made of transparent plastic and so on, with excellent properties of expansion and UV protection of the underlying polycarbonate surface.
Although they guarantee good adhesion to the polycarbonate, the raw materials used do not prejudice the polycarbonate´s mechanical resistance (cracking), but protect it from the otherwise inevitable yellowing followed by decay caused by the powdering of the original UV protection that takes place on average in the course of the first five years of its working life.
Combined with the innovative sanding system, the special three- component formula enables plastics that have been deeply scoured or scratched to be repaired, as long as they are not actually broken.
The headlight reapir system from HBC Smart Repairs offer a fast and easy way to restore the clarity to headlight lenses that have become dull over time, at a fraction of the cost of replacement.
Step by step repair
1. Applying
2. Cleaning
3. Sanding in 3 steps;
remove the complete UV protection
1. Cleaning
2. Mix clear coat
3. Apply 2 layers UV Clear coat
4. Curing 15 min by IR drylamp
5. If needed remove dust or imperfections and polish
Surface Preparation :
> Sand while dry with:
Sky blue (P600) – Lemon (800) – Orange (1500)
It is important that you remove the old protection film from the headlight completely.
For particularly hard surfaces or to remove deep scratches, we recommend that you start sanding with a 320/400 grain, using ø 75 mm discs mounted on a sanding machine.
Mixture (% by weight):
Clear: 100%
Catalyst: 50%
Activator: 50%
> Mix well and filter before using (125 microns)
POT LIFE : 2 hours at 20°C
Application of UV coat:
Coats: 1 + 1 (wait 30 sec. betwee the 2 coats)
Thickness: 30 – 40 microns, dry film
Drying:
In the spray booth at 60 – 70°C: 30 min
Short wave I.R.: 10 - 15 min
INFRA SPOT 1300: 15’ at a distance of 50 – 60 cm
Max. Temp.: 70°- 80°.
Can be dried using a variety of methods: In the spray booth, with an IR lamp or in the air.
Product trade name(s) Headlight Repair System
Product group : D
Part number(s) : 00.609
Expire date : Storage life: 6 months
Content :
Part no. 00.609-1: 250 ml clearcoat
Part no. 00.609-2: 125 ml activator
Part no. 00.609-3: 125 ml catalyst
Abrasives: P400 (2 discs ø75mm),
P600 (4 sky blue sheets 130x85 mm),
P800 4 Lemon sheets 130x85 mm),
P1500 (4 orange sheets 130x85 mm),
Polishing cloth
Typical Properties
Color / Grade of Gloss Transparent and colourless
Characteristics
Special three-component finish with excellent characteristics of resistance and adherence to polycarbonate- base plastic materials, such as lenses for vehicle lights, synthetic glazing ( as long as it is made of polycarbonate), yacht components made of transparent plastic and so on, with excellent properties of expansion and UV protection of the underlying polycarbonate surface.
Although they guarantee good adhesion to the polycarbonate, the raw materials used do not prejudice the polycarbonate´s mechanical resistance (cracking), but protect it from the otherwise inevitable yellowing followed by decay caused by the powdering of the original UV protection that takes place on average in the course of the first five years of its working life.
Combined with the innovative sanding system, the special three- component formula enables plastics that have been deeply scoured or scratched to be repaired, as long as they are not actually broken.
The headlight reapir system from HBC Smart Repairs offer a fast and easy way to restore the clarity to headlight lenses that have become dull over time, at a fraction of the cost of replacement.
Step by step repair
1. Applying
2. Cleaning
3. Sanding in 3 steps;
remove the complete UV protection
1. Cleaning
2. Mix clear coat
3. Apply 2 layers UV Clear coat
4. Curing 15 min by IR drylamp
5. If needed remove dust or imperfections and polish
Surface Preparation :
> Sand while dry with:
Sky blue (P600) – Lemon (800) – Orange (1500)
It is important that you remove the old protection film from the headlight completely.
For particularly hard surfaces or to remove deep scratches, we recommend that you start sanding with a 320/400 grain, using ø 75 mm discs mounted on a sanding machine.
Mixture (% by weight):
Clear: 100%
Catalyst: 50%
Activator: 50%
> Mix well and filter before using (125 microns)
POT LIFE : 2 hours at 20°C
Application of UV coat:
Coats: 1 + 1 (wait 30 sec. betwee the 2 coats)
Thickness: 30 – 40 microns, dry film
Drying:
In the spray booth at 60 – 70°C: 30 min
Short wave I.R.: 10 - 15 min
INFRA SPOT 1300: 15’ at a distance of 50 – 60 cm
Max. Temp.: 70°- 80°.
Can be dried using a variety of methods: In the spray booth, with an IR lamp or in the air.
Monday, January 23, 2012
Customer registration
Manuals, step by step guidance etc. is available for download at our web. However, in order to get access to the customer pages, you’ll have to get registered. It’s simple and easy; just follow the guidance below:
To get registered please click at the following link:
- http://www.hbc-system.com/Registration-5155.aspx
- Fill out the fields (Name, email etc)
- Tick off the system(s) you’ve purchased (This is important – if you don’t tick off you will not be granted access)
- Click at “Register account”
- A message is popping up: Please check your mailbox
- Go to your mailbox and find the confirmation mail ” Smart Repair Tools account registration” from info@hbc-system.com (it might be necessary to check in your mailbox unwanted mails/ Spam mails)
- Click at the highlighted link Approve account. (This is a security to avoid unforeseen access to the website).
- After you have clicked at the hyperlink Approve account your registration is completed. Please keep your login data for future use.
You are now ready to explore the world of HBC Smart Repair !!
Headlight Repair System
Please read more about the new system in this leaflet:
Headlight Repair System
Consisting of a special three-component finish with excellent characteristics of resistance and adherence to polycarbonate-base plastic materials.
The raw materials used do not prejudice the polycarbonate’s mechanical resistance (cracking), but protect it from the otherwise inevitable yellowing.
Combined with the innovative sanding system, the special three-component formula enables plastics that have been deeply scoured or scratched to be restored to former, as long as they are not actually broken.
Headlight Repair system can be ordered online on this link
Saturday, January 21, 2012
Leather Scanner Demonstration
Base colours mixing system for Plastic, Leather & Vinyl Painting System
- soft, hard, and flexible materials
System B3 Aqua works on all flexible, hard and soft materials basecolours for mixing of plastic-, leather- and vinyl colours. Incl. colour swatch, formulas and additives.
Exists as water based. The complete dye to match-system for all soft, hard, and flexible materials such as leather, fabric, vinyl, plastic, and glass fibre. The standard system includes colour swatch, gloss system, mixing book, and primers, etc. All dyes and glosses gain a permanency that makes this system indispensable for service mechanics working with the repair of plastics or with maintenance jobs on furniture, cars, lorries, etc.
Colour matching system with additional spectrophotometer & software
download HBC's scanner information
Friday, January 20, 2012
Texture Coating Kit
Texture coating system and Mouldmaker for leather and plastic from HBC samrt repair
The world’s most complete texture system beats everything on the market. The HBC System Mouldmaker is designed for all types of structure. System B2 includes 5 different spray textures; coarse, medium, fine, fine flat, and coarse flat and 2 types of primers - one clear thin and one with “sanding” that fills in the small scratches and glue holes that often appear.
The world’s most complete texture system beats everything on the market. The HBC System Mouldmaker is designed for all types of structure. System B2 includes 5 different spray textures; coarse, medium, fine, fine flat, and coarse flat and 2 types of primers - one clear thin and one with “sanding” that fills in the small scratches and glue holes that often appear.
Thursday, January 19, 2012
Spot repair, Paint Chip & Car Paint Scratch Repair
Smart Repair Paint Chip Repair System C
It includes all the chemicals and hardware necessary for you to repair a variety of damage and also includes, our Color Match Software and In today’s environment, the best competitive edge is to provide the highest quality repairs.
Equip yourself with the newest technology and deliver unparalleled quality.
With our Paint Color Matching Software, you’ll have direct access to our entire mixing formula database.
Just fill the relevant fields in the clearly structured user interface, and the requested mixing formula will appear on the screen within a wink of an eye - and it’s fast and easy to use.
The database contains over 200.000 mixing formulas, giving access to more than 100.000 colors. It even provides variants of the requested color for badly oxidized or aging paint.
Our Color Match Software is updated four times a year at no additional cost and contains all the MSDS information and safety data sheets for all paint chemicals and toners. As technology changes, so will The HBC system C - Paint Repair Systems.
By anticipating the future, our eco-friendly waterborne line of paint will keep you compliant and one step ahead of your competition.
This system allows you to touch-up and spot repair paint chips and scratches using several different application methods depending upon the type of damage you’re repairing.
It includes all the chemicals and hardware necessary for you to repair a variety of damage and also includes, our Color Match Software and In today’s environment, the best competitive edge is to provide the highest quality repairs.
Equip yourself with the newest technology and deliver unparalleled quality.
- Paint Chips
- Small Scratches
- Chipped Door Edges
- Paint Scratches
- Clear Coat Chips & Scuffs
With our Paint Color Matching Software, you’ll have direct access to our entire mixing formula database.
Just fill the relevant fields in the clearly structured user interface, and the requested mixing formula will appear on the screen within a wink of an eye - and it’s fast and easy to use.
The database contains over 200.000 mixing formulas, giving access to more than 100.000 colors. It even provides variants of the requested color for badly oxidized or aging paint.
Our Color Match Software is updated four times a year at no additional cost and contains all the MSDS information and safety data sheets for all paint chemicals and toners. As technology changes, so will The HBC system C - Paint Repair Systems.
By anticipating the future, our eco-friendly waterborne line of paint will keep you compliant and one step ahead of your competition.
A Wheel smart repair system from HBC system
Polished Aluminium Rim and Wheel Repair system Polished aluminum rim repair system, for the new hot polished aluminum rims –you see them, on the aftermarket and on new cars. With the system you can repair many kind of smaller scratches, parking damaged and other kind of damaged on polished high gloss aluminum rims, aluminum frames on motorbikes, and other aluminum parts. It is an easy to use system, the user do not require to join a training session to be able to start the first repairing jobs. * There are some limits with the kit, like heavy duty deep damaged, some special coatings etc. |
Alloy Wheel Repair System from HBC system
HBC smart repair system Aluminium wheel repair · E3
System E3, Rim repair. For repair of kerbed, scratched or corroded alloy wheels.
It is now possible to repair scratches and damages in aluminium wheels at a very low price and in a very effective manner.
The price of the repair is obviously proportional with the size of the damage, but one thing is certain: repairing wheels is a good bargain.
The system is complete with fillers and aerosol colors for the repair of most common wheel types.
After the application of color, a thick layer of clearcoat is added to attain the perfect finish.
System E3, Rim repair. For repair of kerbed, scratched or corroded alloy wheels.
It is now possible to repair scratches and damages in aluminium wheels at a very low price and in a very effective manner.
The price of the repair is obviously proportional with the size of the damage, but one thing is certain: repairing wheels is a good bargain.
The system is complete with fillers and aerosol colors for the repair of most common wheel types.
After the application of color, a thick layer of clearcoat is added to attain the perfect finish.
Dent repair system for caravans and mobile homes
HBC system have a pattented dent repair system to repair all kind of dents and holes in a caravan wall
With the HBC system E you can repair and recreate all structures and colours...
Caravan smart repair with HBC systems
Why replace the whole side of a caravan just because of a small dent? It is both time-consuming as well as very expensive. With system E you acquire a perfect finish due to specially designed vacuum tools, level-rail, and a specially developed Mouldmaker which recreates the original pattern of the damaged area.
The Press wrote: “Ingenious system for repairing aluminium plates on mobile-homes, caravans, and trailers.”HBC system, developer and manufacturer of smart repair systems mainly for the auto business, has now developed an upgrade system capable of repairing very major damage on aluminium panels.
It is now possible to repair aluminium panels with major damage of up to 3 metres. The system applies to a vast number of rolled relief panels on gates, furniture, buildings, cars and caravans or any surface of a similar construction. With this possibility there are no arguments for not repairing.
Painting of caravans and mobile homes
For maximum colour accuracy we recommend our scanning system. Today our list comprises more than 500 different colours. If we do not have the colour you need, you can send us a sample, we will then scan it and add it to our list, after which it is available for everybody. This service from HBC system is free. Fusion spraying with new and old paint.
We have introduced another innovation – Fade Thinner.
This melts together / dissolves the old and the new paint creating a better finish by eliminating the over spray and spray dust which often necessitates extra polishing to obtain perfect finish.
Caravan primer, white
We have also developed a new white ground colour, this white primer improves the repair job considerably.
Caravan Spot Repair System
Read about Smart Repair Caravan spot repair system (PDF)
System E, (E Starter, E Upgrade and E Complete) Caravan repair.
For the repair of caravans and mobile homes. Copy of structure. HBC has a world wide patent on this.
HBC Caravan repair system
- Innovative
- Professional
- Patented
- Homologated Read more
International users approvals / tests
- Thatcham, UK.
The Motor Insurance Repair Research
- Center / Time studies.
KTI, Germany. Kraftfahrzeug
Technisches Institut. The organisation is owned by 20 German insurance companies.
- DAT system time measurement.
HBC system caravan dent repair system is Innovative Professional Profitable
Wednesday, January 18, 2012
Ozone Air Cleaning
Ozone Air Cleaning http://www.smartrepairtools.com/Air-cleaning-and-air-filtration-5609.aspx Ozone air cleaning for odours in cars and caravans UV-C & OZONE air cleaning Technology is the best odour cleaning Smells can be hard to get rid of. Despite a nicely ventilated room, it can be difficult to get on top of the odours. HBC system H, UV-C & OZONE Technology can - without the use of chemicals - permanently eliminate odour problems of any kind. The odour does not return, unless the pollutant is still present. Elimination of mould fungis up to 99,9% Easy to install! ![]() HBC system H, UV-C & OZONE Technology shall be placed in high areas of the room such as on a bookshelf, wall or on the ceiling. HBC system H, UV-C & OZONE Technology is only to be used, when no persons or animals are in this area, where the system is used. Reasons for choosing the HBC system H You invest in well-being, greater efficiency, an increased job satisfaction and less absence due to illness. Through this technology a number of odour nuisances are being fought, and thereby there is a reduced risk of transmitting infectiously diseases. System H removes the smell from the air; however it also eliminates the odour from for instance the carpets, fabrics, curtains and the walls. Poor indoor climate in the rooms, where people work, affects our quality of life and health in a negative way. It can be anything from malodorous odours from garbage, mould fungis, cigarettes to industrial processes. An unpleasant smell can create discomfort, but indoor the air pollution is a source of headaches, respiratory problems, fatigue, muscle tensions, asthma, allergy, dry mucous membrane and eye irritation. All of this has an influence on the way people work and concentrate during work. HBC system introduces a new machine to fight odour nuisances By using the patented UV-C & OZONE Technology you can eliminate and remove odour nuisance. This technology received the EU Environmental Award, in the category "cleaner technology". Under controlled circumstances UV-C light arises in system H. This light generates/produces ozone (O3) in connection with the natural oxygen (O2) content in the air – this happens in the same way as with sunbeams. By using this method no harmful nitrogen oxides (NOX) arise. This happens, when ozone is being generated by an electric discharge, such as welding or duplicating/copying. Ozone has the ability to combine with organic substances in the air such as Nicotine, and the ozone oxidizes these. Thereby the bacteria, vira and spores present in the air are being eliminated. During the cleaning process the smelling air in the room is being sucked into the system H, and it passes the HBC special lamp. In connection with this, the treated and disinfected air is being led back to the room with an ozone residue. Range of applications Caravan dealers – treatment of smelling caravans and mobile homes Hotels - treatment of hotel rooms, disinfection of the kitchen, removal of odour from smokey bars and treatment of waste sites. Restaurants and discos – odour removal from carpets, fabrics, and furniture after cleaning Nursing homes, smokey rooms, bathrooms, kitchens and waste sites. Building painters – removal of malodorous paint and enamelling jobs. Advantages: A pure physical process without chemicals Advantageous in comparison to filter techniques No negative impact on the environment High operational security Little/minimum maintenance Easy to install Small investment Mobile - movable Range of applications Car dealers – treatment of smelling cars and trucks/lorries This ozone residue "places itself" in for instance walls or fabrics and eliminates the smelling organic substances. In this way the smell is being continuously reduced.
The ozone machine:
Part Number: 00.109 220V Part Number: 00.109 110V HBC system H, UV-C & OZON teknologi, UV-Lamps: 1 x 16W Operating hours (lamps) 8000 Voltage: 110V 230V Power Consumption: 30W Recommended room area: 125m3 Finish: stainless steel Length: 430 mm Width: 130mm High 130 mm Guarantee: 2 years exclusive of the bulb |
Dent removal equipment produced by HBCsystem
Paintless Dent removal equipment produced by HBCsystem
The HBC system PDR (Paintless dent removal) enables an inexpensive repair of small dents without a repaint of the car being necessary - the original paint is preserved.
We apply a special system of highly specialized tools and light. The special ball system enables us to repair damages faster and more gently.
Our special tools are - contrary to other systems - developed exquisitely for American, European and Japanese cars.
Paintless Dent removal steel
We produce the finest PDR tool quality and most price competitive PDR tool set and individual PDR tools in the industry. Including a complete line of adjustable multi angel PDR tools and wale-tale PDR tools.
PDR tools from HBC system is tested and homologated by world fames car producers and PDR technicians
HBC system PDR tools are carefully designed for the professional PDR technician. Each tool size and design fits a logical sequence of use conditions. HBC system PDR tool set the standard industry practices and conditions in the automotive industry with the ergonomics and working ranges required by the dent technician .
The Paintless Dent removal productionThe HBC system PDR production line, use several different kind of high carbon steels in our PDR tools. In quality control testing our material choices far exceed the stainless steel tools in strength.
Our high carbon stainless steel is hard tempered spring steel is costly to produce, but to the serious PDR professional, Tools strength and design will meet your expectations. HBC PDR tools is always, heat cured – heat treated Stainless Steel.
Paintless Dent removal equipmentThe process of heat treating the PDR tools has been developed over years and is the highest Quality in the world, due to millions test by world fames PDR technicians worldwide, and by metal laboratory test after test, to ensure the best quality possible to produce.
Production of Paintless Dent removal equipmentThe HBC system PDR production line, includes the newest steel production machinery including 3D bending machinery. Steels is ordered in coins from leading steel manufactures after the right steel recipe, needed to obtain the right strength, rust protection and last HBC pdr tools must pass the final test – before the tool leave our production. Ready to serve the technician for the next decades.
Test after test, tells us that HBC tools meet your expectations year after year
Test from the tools can also be made to the specifications of single tool diameter